When working with aluminum, the form in which the metal is processed—billet, cast, or forged—can significantly impact the performance, durability, and cost of your final product. Although these forms originate from the same base material, they differ greatly in mechanical properties, production methods, and applications.
In this guide, JXD Machining breaks down the differences between billet, cast, and forged aluminum, helping you make an informed decision for your next project.
What is Billet Aluminum?
Billet aluminum is made by extruding or roll-forming solid aluminum into stock shapes like rods or bars. This form isn’t usually the final product but serves as raw material for further processing—especially CNC machining.
Thanks to its solid, homogeneous grain structure, billet aluminum delivers high strength and excellent precision. This material is ideal for applications requiring tight tolerances and high customization.
Advantages of Billet Aluminum
•High Precision & Customization
Billet aluminum is perfect for CNC machining. Its dense and uniform grain structure ensures components meet tight dimensional requirements with excellent surface finishes.
•Superior Structural Integrity
Billet material has minimal internal defects like porosity or voids, resulting in durable and reliable parts.
•Excellent Thermal Performance
The solid structure enhances heat dissipation, making it ideal for engine parts, heat sinks, and other thermal-sensitive components.
What is Cast Aluminum?
Cast aluminum is produced by melting the metal and pouring it into molds. Once cooled, the aluminum solidifies into the desired shape.
While casting allows for complex geometries, the process often introduces tiny gas bubbles or voids, reducing overall strength compared to billet or forged forms.
Advantages of Cast Aluminum
•Cost-Effective for Large Volumes
Once the mold is created, manufacturers can produce thousands of identical parts at low cost per unit.
•Complex Designs Made Easy
Casting is excellent for producing intricate and irregular shapes that would be costly or impossible with machining or forging.
•Material Efficiency
Leftover metal from casting can often be melted and reused, reducing waste.
•Lightweight with Reasonable Strength
Though not as strong as billet or forged, cast aluminum offers sufficient strength for everyday products, automotive parts, and machinery housings.
What is Forged Aluminum?
Forged aluminum is created by applying extreme compressive forces—through pressing, hammering, or rolling—to solid aluminum, often at elevated temperatures. This process compresses and aligns the grain structure, greatly enhancing strength and durability.
Advantages of Forged Aluminum
•Exceptional Strength and Toughness
The forging process increases tensile strength, yield strength, and fatigue resistance, outperforming both billet and cast aluminum in demanding applications.
•High Impact Resistance
Forged parts are less prone to cracks, fractures, or failures under sudden impact.
•Minimal Defects
Unlike casting, forging eliminates most internal defects, resulting in structurally sound parts.
•Outstanding Fatigue Resistance
Ideal for parts exposed to repetitive stress, such as suspension arms, aircraft components, and heavy-duty machinery.
Billet vs Cast vs Forged Aluminum: Full Comparison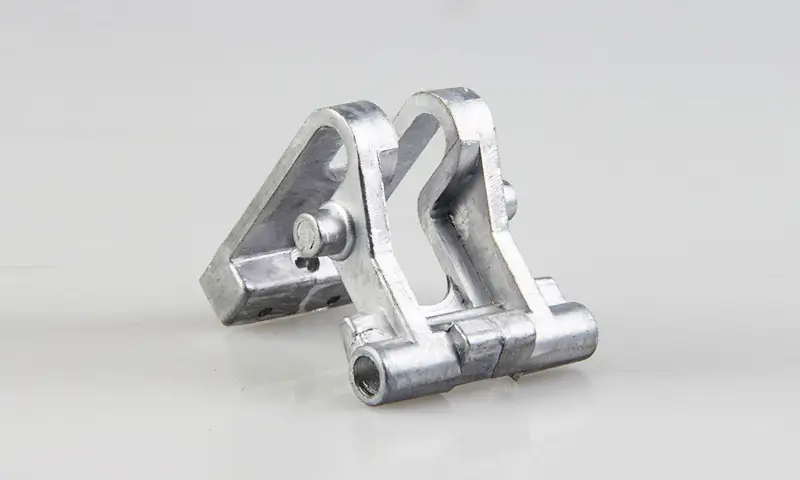
Property |
Billet Aluminum |
Cast Aluminum |
Forged Aluminum |
Strength |
High, better than cast but lower than forged
|
Moderate, affected by porosity
|
Highest, exceptional mechanical strength
|
Machinability |
Excellent, best for CNC machining
|
Good, but defects can affect precision
|
Tougher to machine due to density
|
Surface Finish |
Excellent, minimal post-processing
|
Requires more sanding/polishing
|
More post-processing than billet
|
Cost |
Moderate to High
|
Lowest, ideal for mass production
|
High, due to labor-intensive process
|
Applications |
High-precision parts: aerospace, automotive, robotics
|
Cost-effective consumer goods, machinery housings
|
Structural, load-bearing, or high-impact parts
|
Defect Risk |
Very Low
|
High (porosity)
|
Extremely Low
|
Which Aluminum Type Is Best for Your Project?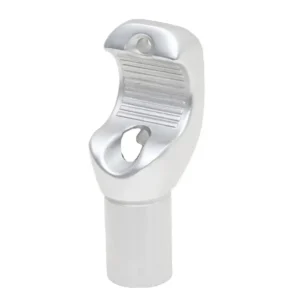
•✅ Choose Billet Aluminum if you need custom, precise parts with tight tolerances and a smooth finish. Perfect for aerospace components, high-end automotive parts, and prototypes.
•✅ Choose Cast Aluminum when cost-efficiency is key, especially for complex shapes produced in large quantities. Suitable for consumer products, housings, and general industrial parts.
•✅ Choose Forged Aluminum for maximum strength, durability, and fatigue resistance. Ideal for structural parts under high load, such as suspension arms, aircraft components, and critical machinery.
JXD Machining: Your Trusted Partner in Aluminum Manufacturing
At JXD Machining, we specialize in providing precision aluminum parts—whether you require billet, cast, or forged components. Our advanced CNC machining services ensure high accuracy, while our engineering team helps you select the right material and process to optimize both performance and cost.
With years of experience serving industries like automotive, aerospace, robotics, and consumer electronics, we are ready to support your next project with reliable, high-quality solutions.
Conclusion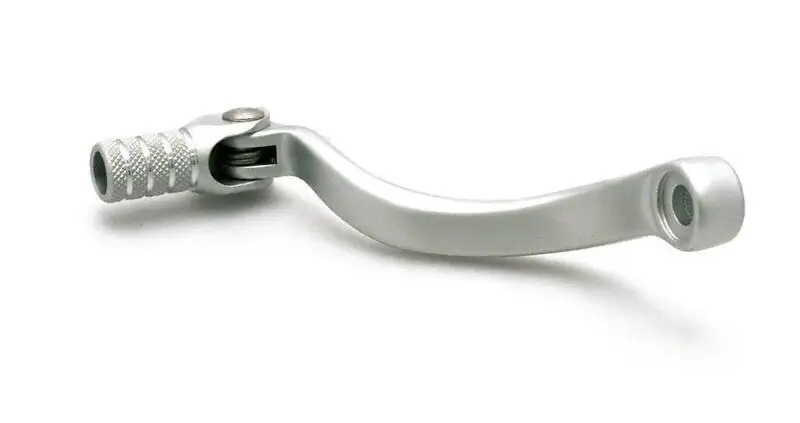
Understanding the differences between billet, cast, and forged aluminum is crucial for selecting the best material for your application. Each offers unique benefits in terms of strength, cost, machinability, and performance.
Partner with JXD Machining to ensure your aluminum parts meet the highest standards for quality and reliability—no matter the complexity.
FAQs
🔧 Which is stronger, billet or forged aluminum?
Forged aluminum is generally stronger than billet because the forging process aligns the grain structure and compresses the material, enhancing strength and durability.
🔧 Is billet aluminum good for structural parts?
Billet aluminum is excellent for high-precision parts requiring accuracy and fine detail but may not match forged aluminum in terms of impact resistance and load-bearing.
🔧 Why choose cast aluminum?
Cast aluminum is the most cost-effective solution for producing complex shapes in large quantities. However, it has lower strength compared to billet and forged.