Ceramic materials (e.g. alumina, zirconia, silicon carbide) are prized for extreme hardness, heat resistance, and chemical stability . These properties make them ideal for high-performance parts in electronics, aerospace, automotive, and medical fields . However, this same hardness and brittleness pose unique machining challenges. In recent years, Ceramic CNC Machining has become a standard approach to fabricate complex ceramic parts with tight tolerances and fine surface finishes . By using multi-axis CNC machines and specialized cutting tools, engineers can now achieve intricate ceramic geometries that older methods struggled to produce.
Types of Ceramic Materials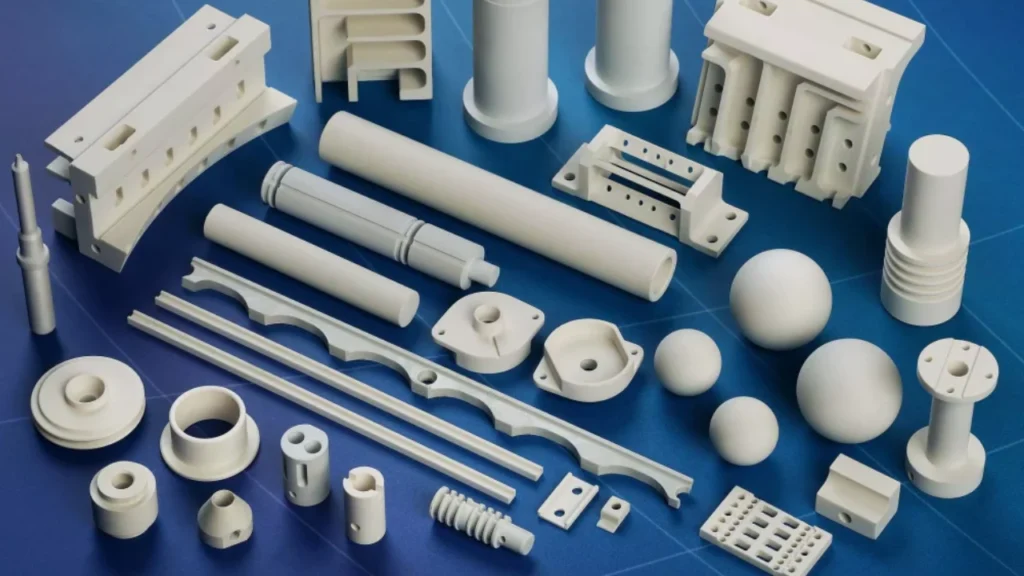
Precision-machined ceramic components (e.g., alumina and boron nitride parts). Ceramic materials vary widely in composition and properties . Each type—like alumina, silicon carbide, or zirconia—offers a different balance of hardness, toughness, and thermal characteristics . These differences dictate the appropriate machining approach for each material. Common engineering ceramics include:
Alumina (Al₂O₃): Extremely hard and wear-resistant, with high temperature tolerance . Machined alumina parts (such as insulating sleeves and cutting tools) exploit its high hardness and corrosion resistance. Ultra-pure alumina is often used for semiconductor substrates and biomedical implants.
Zirconia (ZrO₂): Noted for exceptional toughness and strength . Zirconia’s high fracture toughness and chemical inertness make it valuable in dental/medical implants and wear parts. Its high hardness also enables faster cutting speeds when machined on CNC equipment .
Silicon Carbide (SiC): A superhard ceramic with excellent thermal conductivity and shock resistance . SiC is commonly machined into cutting inserts and heat-dissipating structures. Its high heat conduction helps remove cutting heat, reducing tool wear during machining .
Boron Nitride (BN): A hexagonal ceramic with low dielectric constant and outstanding thermal shock resistance . Compared to oxide ceramics, hexagonal BN is easier to machine and is used for precision substrates, heat exchangers, and electronics components.
Quartz (Fused Silica): Pure SiO₂ with superior optical and electrical properties . It has high tensile strength and thermal stability, but due to its hardness it generally requires diamond tooling or waterjet cutting to machine . Machined quartz parts appear in semiconductor equipment and high-temperature optics.
Each ceramic type requires tailored machining methods to leverage its strengths without causing fractures or tool damage.
Traditional Ceramic Machining Techniques
Before widespread CNC use, ceramic parts were shaped and finished by processes such as:
Sintering and Green Machining: Ceramic powders are pressed and sintered. In the green (unsintered) state, parts can be CNC-machined with carbide or diamond tools, then finally sintered to densify.
Grinding/Lapping: Abrasive grinding wheels or lapping with diamond slurry remove material to near-final dimensions . This achieves tight tolerances and smooth surfaces but is slow and hard on tooling. Fine polishing is often used for final surface finish .
Ultrasonic Machining: A vibrating tool with abrasive slurry removes material from very hard, brittle ceramics without direct mechanical impact, useful for drilling and fine features.
Electrical Discharge Machining (EDM): Spark erosion (EDM) can carve conductive ceramics or carbon-filled ceramics into complex shapes. For example, EDM is used to form silicon-carbide engine valves and bearings for automotive uses . It cuts without direct force, avoiding fractures in extremely hard ceramics.
Laser/Waterjet Cutting: High-power lasers or abrasive waterjets cut ceramic slabs into rough shapes. For instance, aerospace parts often begin with laser-cut blanks and ultrasonic finishing to yield lightweight, precise components .
These conventional methods often involve multiple steps and careful handling, since ceramics are prone to cracking from mechanical stress . Hybrid approaches (e.g. combining grinding and EDM) are common to balance precision and cost.
CNC Machining Processes
CNC machining applies computer-controlled milling, turning, or grinding to form ceramic parts. A typical CNC process includes :
1.Design & CAM: The part is modeled in CAD. CAM software generates G-code with precise toolpaths.
2.Setup: A sintered or green ceramic blank is rigidly fixtured in the CNC machine. Soft jaws, vacuum chucks, or special clamps prevent stress on the brittle material.
3.Rough Machining: Coarse diamond-coated endmills or form tools remove the bulk of material at moderate feed rates.
4.Finish Machining: Fine passes with high-speed, small-diameter diamond tools achieve the final dimensions and surface finish.
5.Inspection: The finished ceramic part is measured (often with CMM or optical gauges) to verify dimensional accuracy.
Multi-axis CNC milling of a cylindrical ceramic workpiece using a diamond tool. Modern 4- or 5-axis CNC centers enable complex ceramic shapes with high precision . For example, simultaneous milling on five axes can cut angled features or holes that would be impossible with simpler machines. Rigid machine frames and high-power spindles minimize deflection and vibration. In many cases, ceramic materials machining is done wet (with coolant) to remove debris and cool the cutting zone, although dry machining is used when keeping parts clean of moisture is critical. Proper CNC process planning – including toolpath strategies like trochoidal milling to reduce force – is essential to avoid chipping.
Tooling for Machining Ceramics
Selecting the right cutting tool is critical for ceramic CNC machining . The hardest tool materials are used to cut ceramic materials:
Diamond Tools: Diamond-coated or polycrystalline diamond (PCD) cutters and grinding wheels provide superior hardness and wear resistance . They produce the best surface finish on oxides and nitrides. Diamond endmills, drills, and saws are standard for precision ceramic machining.
Tungsten Carbide Tools: Carbide tools (often with diamond coatings) are used for roughing or less critical cuts . Carbide is tougher (less brittle) than diamond but will wear faster. It is used where some tool wear is acceptable or cost must be lower.
Silicon Nitride (Si₃N₄) Tools: Silicon nitride cutting inserts or nozzles are valued for their thermal stability under high-speed machining . They maintain strength at elevated temperatures and resist thermal shock, beneficial for extended roughing runs.
Cubic Boron Nitride (CBN) Tools: CBN is nearly as hard as diamond and is often used in sintered abrasive tools for ceramic grinding . It excels in machining very hard silicon nitride or boron carbide ceramics that might quickly dull diamond tools.
In general, tools for ceramics have very sharp cutting edges and often incorporate grit (abrasives) in the bonding matrix. Coolant delivery to the cutting zone is carefully controlled to reduce heat; high-pressure water or oil may be used to flush out hard ceramic chips, which can be abrasive themselves.
Post-Processing and Finishing
After CNC machining, additional steps improve the ceramic part:
Stress Relieving: A low-temperature bake or anneal can alleviate subsurface stresses introduced during cutting . This reduces the risk of cracks growing when the part is in service.
Fine Grinding/Polishing: Surfaces are often ground or polished with diamond abrasives to remove any micro-cracks and achieve the final smoothness. As noted, “precision grinding and polishing” are essential for ceramic substrates in electronics .
Coating/Glazing: Some parts receive thin coatings (e.g. glaze, PVD) to enhance wear resistance or biocompatibility. For instance, medical ceramic implants may be polished to a mirror finish or coated with biocompatible layers.
Inspection & Cleaning: Dimensional checks ensure tolerances are met. High-magnification inspection (or interferometry) can detect minute surface flaws. Machined ceramic dust (silica) is hazardous, so thorough cleaning (often ultrasonic cleaning) is performed to remove all debris.
These post-machining processes ensure the ceramic component meets its strict functional requirements, whether that is optical clarity, electrical insulation, or biocompatibility.
Challenges and Solutions
Machining ceramics presents several challenges :
Extreme Hardness: Ceramics (especially alumina, SiC, Si₃N₄) quickly dull cutting tools . Tool life can be measured in minutes.
Brittleness: Unlike metals, ceramics do not deform plastically. They will crack or fracture if overloaded . A single heavy cut can destroy a part.
Heat Buildup: Low thermal conductivity traps heat at the cutting edge. This can induce thermal cracks in the ceramic and degrade tools .
Surface Integrity: Achieving a smooth finish is hard because even small chipping creates subsurface damage and roughness .
Industry practice overcomes these issues with tailored strategies :
Advanced Tool Materials: Diamond-coated and ceramic-based cutting tools resist wear and heat . Using the sharpest possible cutting edges minimizes chipping.
Optimized Parameters: Machining is done at lower speeds and feeds than metals. Shallow depth-of-cut and pecking motions are used to gradually remove material .
Coolant and Lubrication: Flood coolant or high-pressure coolant flushes away hot chips and reduces friction . In some cases, cryogenic cooling (liquid nitrogen) is used to eliminate thermal shock.
Rigid Fixturing and Damping: Sturdy workholding and anti-vibration fixtures prevent chatter. Preloading or damping systems can absorb cutting vibrations so the part does not crack .
Post-Machining Treatments: Thermal stress relieving cycles and precise polishing help “heal” any minor cracks and improve surface quality .
By integrating these solutions, manufacturers can reliably produce complex ceramic components despite the material’s difficulties.
Industry Applications
Zirconia ceramic screws — examples of high-precision machined ceramic components. Machined ceramics play vital roles across industries . Key applications include:
Aerospace & Defense: Lightweight, heat-resistant ceramics are used for engine components, thermal shields, and RF windows. CNC laser cutting and ultrasonic machining create intricate ceramic parts (e.g. turbine blades, radomes) that reduce weight and improve performance .
Electronics & Semiconductors: Ceramic substrates, insulators, and heat sinks are machined to micron tolerances. Precision grinding and polishing yield the smooth, flat surfaces required for semiconductor wafers and circuit boards .
Medical Devices: Bioceramics (alumina, zirconia) are machined into implants and surgical tools. For example, zirconia hip-joint components and dental crowns are cut with diamond tooling to exact shapes, producing wear-resistant, biocompatible parts .
Automotive: Hard ceramic valves, seals, and sensor housings (often silicon carbide or nitride) withstand high temperatures and wear. Electrical discharge machining (EDM) is used to cut complex SiC parts for engines and high-performance brakes .
Energy & Photonics: Ceramic components are critical in fuel cells, batteries, and optical devices. For instance, zirconia fasteners and connectors (as shown above) offer excellent insulation and chemical resistance in harsh environments .
Each example leverages CNC machining of ceramics to create parts that metal machining cannot easily replace. As shown in multiple case studies , the precision and material properties of ceramic parts often lead to superior durability and performance.
Conclusion
Ceramic CNC machining combines advanced machine tools, cutting-edge tooling, and precise process control to fabricate parts from extremely hard, brittle materials . By carefully selecting tools and parameters, manufacturers can machine complex ceramic components with high accuracy. Ongoing advances in cutting tool materials (like novel diamond composites) and machine design continue to expand what is possible. In high-tech industries from aerospace to biomedical, ceramic materials machining now produces components that are lighter, harder, and more heat-resistant than metal parts, driving innovation in engineering design . As demand grows for specialized ceramic parts, ceramic CNC machining will remain a cornerstone technology for high-performance manufacturing.
Sources: Recent industry and technical publications have informed this guide . These include materials provided by leading ceramic manufacturers and machining experts.