In the realm of precision machining, both conventional turning and Swiss CNC machining offer distinct approaches to creating high – quality parts. For mechanical designers aiming to bring their innovative concepts to life and for procurement professionals seeking the most cost – effective and high – quality manufacturing solutions, understanding when to choose Swiss CNC machining over conventional turning is crucial. This blog post will explore the fundamental differences between these two machining processes, compare them across various key aspects, and provide real – world examples to guide decision – making.
Understanding the Basics: Conventional Turning vs Swiss CNC Machining
Principles of Conventional Turning
Conventional turning is a machining process where a workpiece is rotated on a spindle, and a single – point cutting tool removes material from the surface of the workpiece. The cutting tool moves along two main axes, the X – axis (radial direction) and the Z – axis (axial direction). The rotation of the workpiece and the movement of the cutting tool are coordinated to create cylindrical shapes, such as shafts, pins, and bushings. This process has been a staple in the manufacturing industry for decades and is relatively straightforward in its operation. For example, in a typical automotive engine manufacturing plant, many of the engine shafts are produced using conventional turning. The lathe operator programs the movement of the cutting tool to precisely shape the raw material into the desired shaft dimensions.
Principles of Swiss CNC Machining
Swiss CNC machining, also known as Swiss – type machining or Swiss – style machining, is a specialized form of CNC turning. It uses a sliding headstock lathe with a guide bushing. The bar stock is fed through the guide bushing, which supports the material close to the cutting tool. This setup allows for the machining of long, slender parts with minimal deflection. The workpiece can move along the Z – axis while being rotated, and multiple cutting tools can operate simultaneously. Swiss machining was initially developed for the watchmaking industry in Switzerland to produce small, intricate parts. Today, it has found applications in a wide range of industries, from medical to aerospace. In a medical device manufacturing facility, for instance, Swiss machining might be used to create tiny, high – precision components for surgical instruments. The guide bushing ensures that the slender workpieces are held firmly during the machining process, enabling the creation of complex shapes with high accuracy.
Comparative Analysis
Suitable Part Types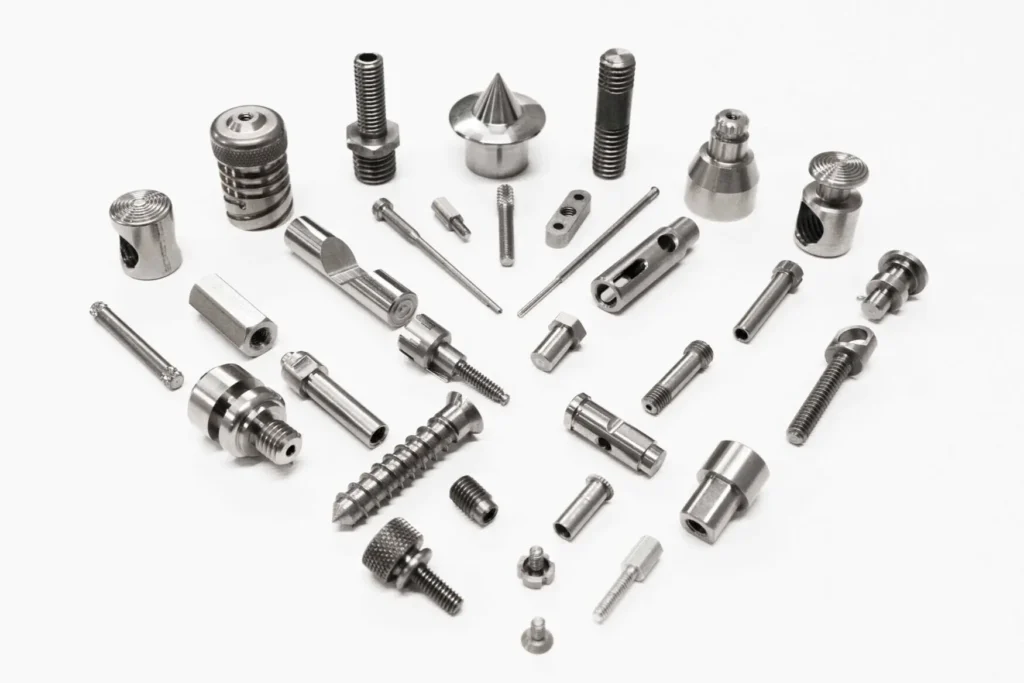
Miniature Parts
- Conventional Turning: While conventional turning can produce small parts, it has limitations when it comes to extremely miniature components. The setup and tooling for very small parts can be challenging, and achieving high precision can be difficult due to the relatively large size of the cutting tools and the lack of support for the workpiece in close proximity to the cutting point.
- Swiss CNC Machining: Swiss machining is ideal for miniature parts. The guide bushing provides excellent support for small – diameter bar stock, allowing for the creation of parts with diameters as small as a few millimeters. In the electronics industry, Swiss – type lathes are often used to produce tiny connectors and pins with high precision. For example, the connectors used in high – end smartphones, which need to be small yet highly reliable, are frequently manufactured using Swiss CNC machining.
Long and Slender Parts
- Conventional Turning: Machining long and slender parts with conventional turning can be problematic. The unsupported length of the workpiece can cause deflection during the cutting process, leading to inaccuracies in the final part. As the length – to – diameter ratio of the workpiece increases, the risk of deflection also increases.
- Swiss CNC Machining: Swiss machining excels at producing long and slender parts. The guide bushing supports the workpiece along its length, minimizing deflection. This makes it possible to machine parts with high length – to – diameter ratios. In the aerospace industry, for example, long, slender shafts used in aircraft engines can be accurately machined using Swiss CNC machining. The ability to maintain the straightness and dimensional accuracy of these shafts is crucial for the performance and reliability of the engine.
Complexity of Parts
- Conventional Turning: Conventional turning is well – suited for producing parts with simple cylindrical geometries. However, creating parts with complex features, such as cross – drilled holes, multiple angles, and non – circular profiles, can be extremely difficult or may require multiple setups and additional operations.
- Swiss CNC Machining: Swiss machining can handle complex part geometries with ease. Multiple tools can operate simultaneously, allowing for the creation of features like cross – drilled holes, milled slots, and threaded sections in a single setup. In the production of medical implants, which often have complex shapes and features to fit the human body precisely, Swiss CNC machining is the preferred choice. For example, hip implant components with intricate surface features and precise dimensions can be manufactured using this process.
Precision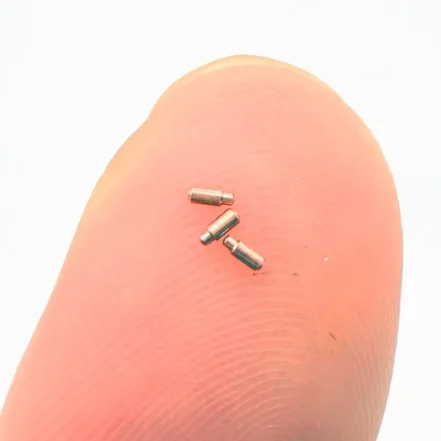
Conventional Turning: Conventional turning can achieve a relatively high level of precision, typically within ±0.05mm in many cases. However, factors such as tool wear, workpiece deflection, and machine vibration can affect the final accuracy, especially when machining complex or long parts.
Swiss CNC Machining: Swiss machining is renowned for its exceptional precision. It can achieve tolerances as tight as ±0.005mm or even better. The support provided by the guide bushing and the ability to control multiple axes precisely contribute to this high level of accuracy. In industries like aerospace and medical, where even the slightest deviation can have significant consequences, Swiss CNC machining’s precision capabilities make it the go – to option. For example, in the production of aerospace components such as fuel injector nozzles, which require extremely precise dimensions to ensure proper fuel atomization and engine performance, Swiss machining is used to meet the tight tolerance requirements.
Cost Structure
Equipment Investment
- Conventional Turning: Conventional turning machines are generally less expensive to purchase compared to Swiss CNC machines. The basic structure of a conventional lathe is simpler, with fewer axes and less complex tooling systems. This makes them more accessible for small – to – medium – sized manufacturing shops with limited budgets.
- Swiss CNC Machining: Swiss machining centers are more costly due to their specialized design and advanced features. The sliding headstock, guide bushing, and multi – axis control systems add to the complexity and cost of the machine. However, for high – volume production of precision parts, the long – term cost – effectiveness of Swiss machining can offset the initial investment.
Unit Cost
- Conventional Turning: For small – volume production runs, the unit cost of parts produced by conventional turning can be relatively low, considering the lower equipment cost and simpler setup. But as the complexity of the part increases, the need for multiple setups and longer machining times can drive up the unit cost.
- Swiss CNC Machining: In high – volume production, Swiss machining can offer lower unit costs. The ability to perform multiple operations in a single setup and the high production speed reduce the overall machining time per part. Additionally, the high precision of Swiss machining often eliminates the need for secondary operations, further reducing costs. However, for very small production runs, the high initial investment in the machine may result in a relatively high unit cost.
Processing Efficiency
Conventional Turning: Conventional turning machines typically operate as single – station systems. Each operation, such as turning, drilling, or threading, is performed sequentially. This can lead to longer cycle times, especially for parts that require multiple operations. For example, if a part needs to be turned, drilled, and threaded, the workpiece has to be moved to different stations or the machine has to be reconfigured between each operation.
Swiss CNC Machining: Swiss machines are often equipped with multiple tool stations and can perform multiple operations simultaneously. This multi – station capability significantly reduces cycle times. For instance, a Swiss – type lathe can turn the outer diameter of a part, drill a hole, and mill a slot all at the same time. In high – volume production scenarios, this can lead to a substantial increase in productivity. A manufacturer producing thousands of small, complex parts for the electronics industry can benefit greatly from the high processing efficiency of Swiss CNC machining.
Material Adaptability
Conventional Turning: Conventional turning can work with a wide range of materials, including metals such as steel, aluminum, and copper, as well as plastics. However, when machining hard or exotic materials, tool wear can be a significant issue, and special tooling may be required.
Swiss CNC Machining: Swiss machining is also highly adaptable to different materials. It can handle metals like stainless steel, brass, titanium, as well as various plastics such as nylon and polycarbonate. The support provided by the guide bushing allows for stable machining of materials that may be difficult to work with in a conventional turning setup. For example, when machining long, slender titanium rods for aerospace applications, Swiss CNC machining can ensure accurate and efficient material removal without excessive tool wear.
The following table summarizes the key differences between conventional turning and Swiss CNC machining:
Aspect
|
Conventional Turning
|
Swiss CNC Machining
|
Suitable Part Types
|
Good for simple cylindrical parts. Challenging for miniature, long – slender, and complex parts.
|
Ideal for miniature, long – slender, and complex parts.
|
Precision
|
Usually within ±0.05mm.
|
Can achieve ±0.005mm or better.
|
Cost Structure – Equipment
|
Lower initial investment.
|
Higher initial investment.
|
Cost Structure – Unit Cost
|
Low for small – volume, simple parts. Can increase with complexity.
|
Lower for high – volume production due to efficiency.
|
Processing Efficiency
|
Single – station, sequential operations. Longer cycle times for complex parts.
|
Multi – station, simultaneous operations. Shorter cycle times.
|
Material Adaptability
|
Works with a wide range of materials, but tool wear can be an issue with hard materials.
|
Highly adaptable to various materials, including hard and exotic ones.
|
Common Application Areas of Swiss Machining
Medical Industry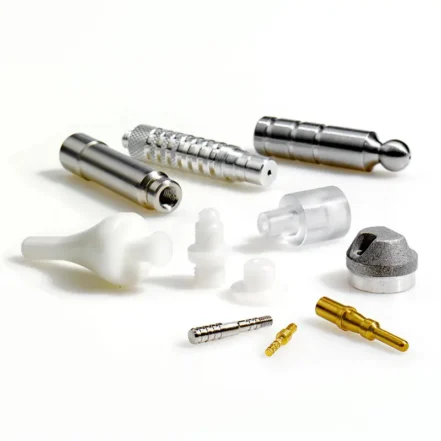
In the medical field, Swiss machining is widely used to produce high – precision components for surgical instruments, implants, and diagnostic equipment. The ability to create parts with extremely tight tolerances is crucial for ensuring the safety and effectiveness of medical devices. For example, the small, intricate components of a laparoscopic surgical instrument need to be precisely machined to allow for smooth and accurate operation inside the human body. Implants such as hip and knee replacements also require high – precision manufacturing to ensure a proper fit and long – term functionality.
Aerospace Industry
The aerospace industry demands parts with the highest level of precision and reliability. Swiss machining is used to produce components for aircraft engines, avionics systems, and landing gear. Parts such as turbine blades, fuel injector components, and fasteners are often manufactured using Swiss CNC machining. The ability to machine long, slender parts with minimal deflection is particularly useful in aerospace applications, where the weight and performance of components are critical factors.
Electronics Industry
In the electronics industry, Swiss machining is used to produce small, high – precision parts for devices such as smartphones, tablets, and wearables. Connectors, pins, and small shafts are some of the components commonly manufactured using Swiss machining. The process enables the production of parts with small dimensions and complex geometries, which are essential for the miniaturization and functionality of modern electronic devices.
Conclusion and Advice for Customers
When choosing between Swiss CNC machining and conventional turning, mechanical designers and procurement professionals should consider several factors. First, the nature of the part itself is crucial. If the part is small, slender, or complex, Swiss machining is likely the better option. Second, precision requirements must be carefully evaluated. If tight tolerances are essential, Swiss machining’s high – precision capabilities make it a clear choice. Third, production volume and cost considerations play a role. For high – volume production, Swiss machining can offer cost – effective solutions despite the higher initial equipment investment.
When communicating with manufacturers, customers should provide detailed information about the part design, including dimensions, tolerances, surface finish requirements, and the intended application. This information will help the manufacturer determine the most suitable machining process and provide an accurate quote. Additionally, customers should discuss the production volume and expected delivery time, as these factors can also influence the choice of machining method. By working closely with the manufacturer and providing comprehensive information, customers can ensure that they receive the best – quality parts at a reasonable cost, whether through Swiss CNC machining or conventional turning.